Materials
All JIS-B 6339 / MAS 403 BT Toolholders are made of case-hardened steel. The supply of the material, made by the main Italian steel mills, is accompanied by the 3.1 UNI EN 10204 certifications.
Thermal treatments
A carburization is carried out with a depth of 0.4 - 0.5 mm in order to achieve a value of HRC hardness of 58 ± 2 and a tensile strength of 800-1000 N / mm2.
Grinding
After the burnishing, the parts are grinded externally and internally, including the threads of the nuts that tighten the collet.
Quality
Tolerance of the cone
The taper complies to the AT3 class according to DIN standards and to the following table:
ISO | L | dA - dB | AT3 |
30 | 42 | 12.250 | + 0.002 |
40 | 59 | 17.208 | + 0.003 |
50 | 92 | 26.833 | + 0.004 |
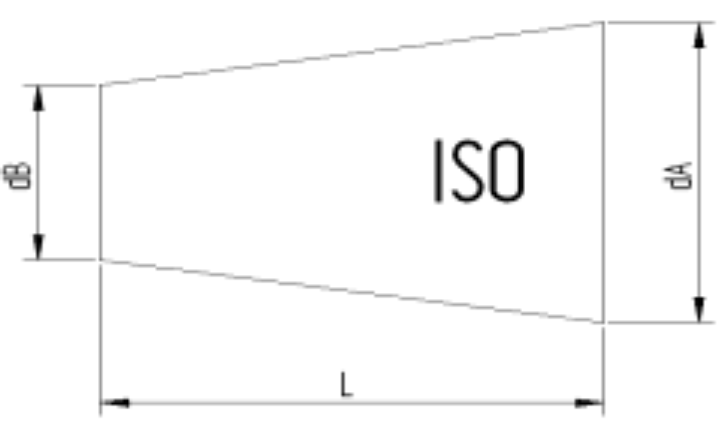
Balancing
In accordance with company's internal quality procedures, balancing is performed almost for each toolholder of this product family, using Haimer Balancing Machines in class G 6.3 at 12000 rpm for 1 min.
Coaxiality
Collet Chucks
Against the maximum runout deviation in DIN 6391, equal to 0.016 mm for both DIN6499 and DIN 6388 Collet Chucks, our production shows eccentricity values, between ISO cone and collet seat, ranging between 0.003 and 0.010 mm.
Shell End Mill Adaptors
According to DIN 6358, the Pagnoni Shell End Mill Holders have a maximum coaxial error, between ISO 30 and ISO 40 tapers and the diameters 16/22/27/32/40 equal to 0.01 mm, while for ISO 50 the maximum error allowed is 0.015 mm.
Weldon / Whistle Notch End Mill Holders
In compliance with DIN 6359-1, the hole is made in tolerance class H5, with an average coaxiality value of 0.005 mm, where the maximum runout deviation allowed between the cone and Weldon seat is <0.01 for="" iso="" 40="" p="">
Quality of production
We perform accurate tests on 100% of our production through certified instrumentation:
- Certified AT3 taper control, by Stotz pneumatic gauges
- Checking of threads and seats with taper clamps and collet holder, with MG Calibri gauges